Heroes MAKE America Graduate’s Manufacturing Career Takes Flight
"Once I got to the description of Heroes MAKE America, I knew that was what I wanted to do."
Joseph Smith spent 20 years in the military, beginning as a mechanic working on Apache helicopters and serving for most of his career as a maintenance supervisor in the U.S. Army. Today, he’s a maintenance unit supervisor based in Davenport, Iowa, at Arconic—a worldwide light metals manufacturer creating products for sectors from aerospace to consumer electronics.
Initially, Smith didn’t know how he’d adapt to civilian life after two decades in the military, but he was immediately impressed with The Manufacturing Institute’s Heroes MAKE America program, which aims to connect manufacturers with highly qualified candidates and offer transitioning service members manufacturing-related training and support, creating a pipeline between the military and manufacturing.
“I was trying to decide what I wanted to do after the military,” said Smith. “I was looking into the different programs and apprenticeships the army offered, and once I got to the description of Heroes MAKE America, I knew that was what I wanted to do.”
Smith grew up interested in how things are made. “I used to watch that How It’s Made series on TV,” he said. For him, his new job makes sense. He still enjoys watching how aluminum is made from raw material and seeing it become a finished product like the wing of an airplane.
“There’s so much that goes into the products that we use and the things we see on a daily basis,” he said.
Smith has been impressed by the similarities between his role in the military and his current position. While the transition to civilian life could have been challenging after two decades in the military, he immediately found manufacturing was uniquely suited to his skills.
“I could almost instantly tell,” Smith said. “The way that the maintenance portion of Arconic runs was very similar to, day-to-day, how working in the military was.”
Smith encourages other veterans to consider making the same move he did and emphasizes the number of jobs available to skilled workers.
“There are a lot of people who don’t realize how valuable a career in manufacturing can be,” says Smith. “Especially for a veteran coming out of the military, they don’t realize how in-demand their skills can be. Everything you do can be translated into a manufacturing career. And manufacturing employers are hiring like crazy.”
Learn more about the Manufacturing Institute’s Heroes MAKE America program.
NAM Survey: Manufacturing Optimism Dips in Q2 Amid Trade Uncertainties, Workforce Shortage
Urgent Action Needed on USMCA, Other Priorities to Boost Manufacturing Growth
Washington, D.C. – The National Association of Manufacturers today released the results of the Manufacturers’ Outlook Survey for the second quarter of 2019. In the field during the prospects of tariffs on Mexican goods and still unresolved threat of 232 auto tariffs, the survey shows a dip in manufacturers’ optimism amid trade uncertainties. A positive outlook for their business was registered by 79.8 percent of manufacturers in the second quarter, down from 89.5 percent in the first quarter.
“Clearly, optimism is still strong among manufacturers, but you can’t overlook the fact that trade uncertainties are causing concern for manufacturers,” said NAM Chief Economist Chad Moutray, who conducted the survey. “All things equal, I would expect these numbers to improve if we get the U.S.–Mexico–Canada Agreement across the finish line, strengthen our trading relationships by removing the threat of 232 auto tariffs and get a trade deal with China done.”
The inability to attract and retain a quality workforce remained manufacturers’ top business concern (68.8 percent) in the second quarter. The survey also found that a majority of manufacturers (56 percent) are concerned about trade uncertainties with regards to the USMCA, a U.S.-China trade agreement, looming 232 auto tariffs and the now-resolved threat of U.S. tariffs on Mexico. In addition, nearly half of manufacturers are concerned about increased raw material prices.
The Manufacturers’ Outlook Survey has surveyed the association’s membership of 14,000 large and small manufacturers on a quarterly basis since 1997 to gain insight into their economic outlook, hiring and investment decisions and business concerns. The NAM releases the results to the public each quarter. Further information on the survey is available here.
-NAM-
The National Association of Manufacturers is the largest manufacturing association in the United States, representing small and large manufacturers in every industrial sector and in all 50 states. Manufacturing employs more than 12.8 million men and women, contributes $2.38 trillion to the U.S. economy annually, has the largest economic multiplier of any major sector and accounts for more than three-quarters of private-sector research and development. The NAM is the powerful voice of the manufacturing community and the leading advocate for a policy agenda that helps manufacturers compete in the global economy and create jobs across the United States. For more information about the Manufacturers or to follow us on Shopfloor, Twitter and Facebook, please visit www.nam.org.
Heroes MAKE America Student Makes Tracks at Goodyear
“As manufacturing goes more autonomous, there are more skilled positions available.”
Jason Gustine has always enjoyed learning how things are made. As an area manager at the Goodyear Tire & Rubber Company in Topeka, Kansas, he taps into his lifelong interest while making use of the people skills and the processes he learned in the military.
“I was worried it would be a culture shock, and I wasn’t going to fit in,” said Gustine. “But going into a manufacturing facility, it fits exactly with the military mindset. That was the biggest surprise—how easy that transition was.”
Military service runs in Gustine’s family. His father is a former helicopter pilot who served in Vietnam, and Gustine was determined to follow in his father’s footsteps. He joined the U.S. Army in January 2008 and served 11 years in the military—as a mechanic, a Blackhawk crew chief, a standardization instructor and eventually a leader in quality control, making sure helicopters were safe to fly.
When he was beginning the transition out of military service, Gustine joined up with the Manufacturing Institute’s Heroes MAKE America program, which aims to connect manufacturers with highly qualified candidates and offer transitioning service members manufacturing-related training and support, creating a pipeline between the military and manufacturing. Through the program in Fort Riley, Kansas, he realized that manufacturing was a perfect next step for him.
“It fit into my wheelhouse,” he said. “A lot of it was maintenance and mechanics, which I’d been doing my whole life. Making sure that the product they’re sending out is the right quality. And every Friday, we would go tour a different facility. That’s what opened my eyes to what manufacturing had to offer.”
He credits the Heroes MAKE America program with helping to smooth the transition out of the military.
“Getting out of the military is a very stressful time,” he said. “I had all these skills—I had worked on helicopters for 10 years—but I didn’t really know how that was going to transition to the civilian world.”
Gustine has been impressed with the way manufacturing has integrated high-tech processes into daily operations without lessening the need for skilled employees, and the industry continues to emphasize the need for new workers.
“People have this idea that it’s all automated now, which is not true at all,” he said. “As manufacturing goes more autonomous, there are more skilled positions available.”
Gustine is enthusiastic about what manufacturing has to offer and encourages other service members to consider the wide range of available roles.
“The manufacturing field is so big—you can do everything from making tires in Topeka to building cars in Ohio,” Gustine said. “Whatever you want to do, you can find your niche or find your spot. It opened my eyes to how much manufacturing there is in the United States. Find out where you want to go, and the sky is the limit in manufacturing.”
Learn more about the Manufacturing Institute’s Heroes MAKE America program.
NAM Statement on Second Meeting of the American Workforce Policy Advisory Board
Washington, D.C. – National Association of Manufacturers President and CEO Jay Timmons released the following statement on the second meeting of the American Workforce Policy Advisory Board:
Manufacturers’ top challenge is finding and recruiting talented workers, and The Manufacturing Institute is meeting this challenge through programs like Heroes MAKE America and the STEP Women’s Initiative to bring more women, veterans and young people into our industry. We are proud to share these solutions and insights with the American Workforce Policy Advisory Board and to work together to identify and develop additional innovative solutions to build the strongest workforce in history.
Background
The American Workforce Policy Advisory Board, chaired by Ivanka Trump and Commerce Secretary Wilbur Ross, was established by the Department of Commerce pursuant to Executive Order 13845, Establishing the President’s National Council for the American Worker. The Board will provide advice and recommendations on ways to encourage the private sector and educational institutions to combat the skills crisis by investing in and increasing demand-driven education, training and re-training, including training through apprenticeships and work-based learning opportunities.
Timmons was nominated to serve on the American Workforce Policy Advisory Board in September by Carolyn Lee, executive director of The Manufacturing Institute, the workforce and education partner of the NAM. Timmons also serves as Chairman of the Board of The Manufacturing Institute. According to a landmark 2018 study conducted by The Manufacturing Institute and Deloitte, 2.4 million manufacturing jobs are expected to go unfilled over the next decade.
-NAM-
The National Association of Manufacturers is the largest manufacturing association in the United States, representing small and large manufacturers in every industrial sector and in all 50 states. Manufacturing employs more than 12.8 million men and women, contributes $2.38 trillion to the U.S. economy annually, has the largest economic multiplier of any major sector and accounts for more than three-quarters of private-sector research and development. The NAM is the powerful voice of the manufacturing community and the leading advocate for a policy agenda that helps manufacturers compete in the global economy and create jobs across the United States. For more information about the Manufacturers or to follow us on Shopfloor, Twitter and Facebook, please visit www.nam.org.
Heroes MAKE America Student Goes from the Army to Mars
An Army veteran's skills translate seamlessly in the manufacturing industry.
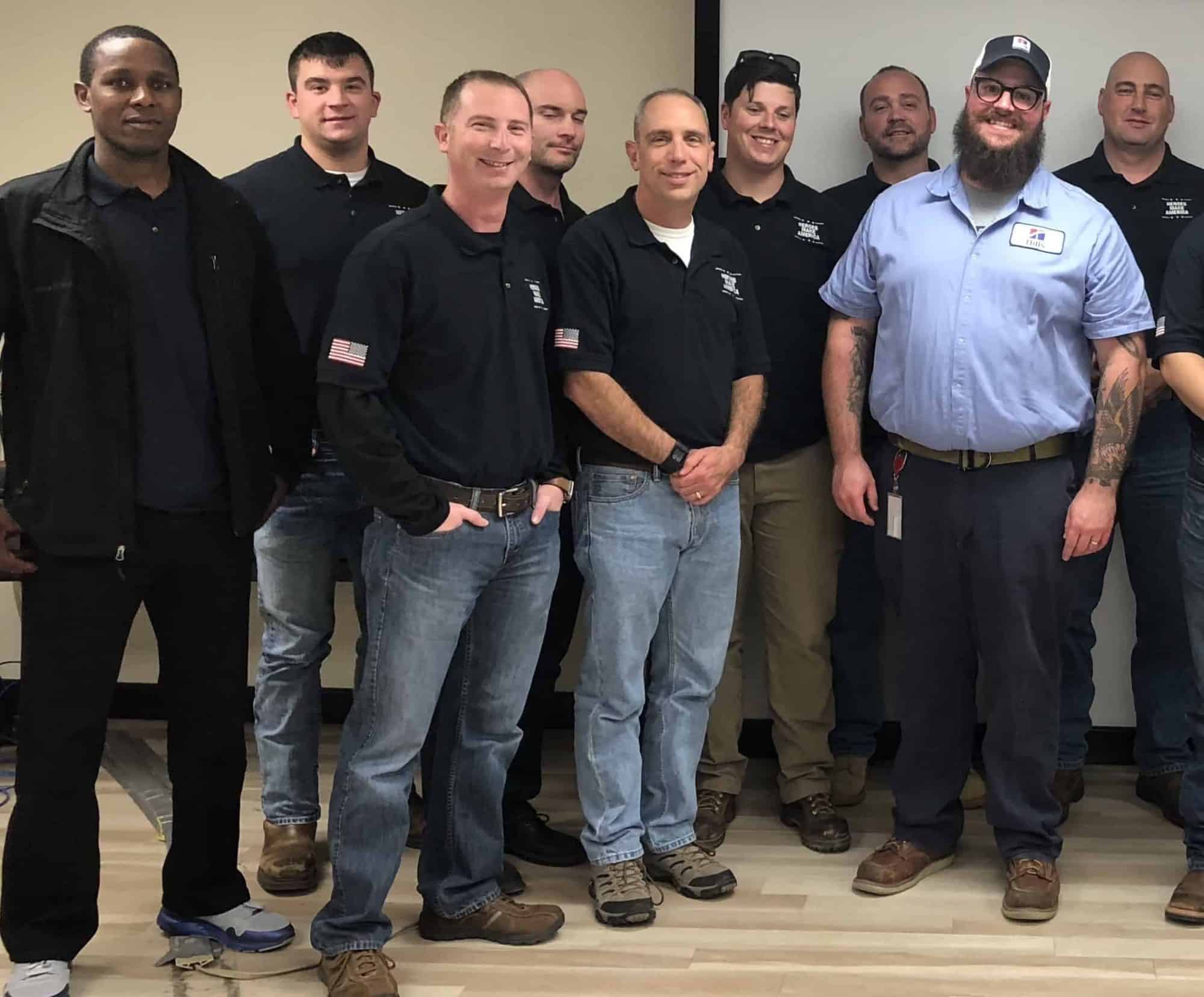
As a production scheduler for Mars, Incorporated, Thomas Schlieper has a hand in sending sweet treats all over the world.
In some ways, it’s very different from his former career. As a teenager, Schlieper joined the Army National Guard because it offered benefits like tuition assistance and scholarships that would help him go to college. When he finished school, he worked in his hometown and eventually decided to go into active service in the U.S. Army. That career spanned two decades and helped lead him to the manufacturing job he enjoys today.
While Schlieper served as an Army senior supply specialist, he enrolled in the Manufacturing Institute’s Heroes MAKE America program, which aims to connect manufacturers with highly qualified candidates and offer transitioning service members manufacturing-related training and support, thus creating a pipeline between the military and manufacturing. Through this U.S. Department of Defense-approved program, he toured the Mars production facility in Topeka, Kansas. Mars recognized his logistics experience and offered him a production scheduler position, which he accepted in February 2019.
“I served 20 years as a logistics guy,” he said. “Ordering supplies, making sure soldiers in the Army had what they needed. The leadership skills I learned in the Army helped me adapt to this new role.”
Schlieper recalls the stress he felt during his first day on the job at Mars, when he wondered whether he was up to the challenges of his new role—and the moment when it all clicked.
“My first couple days there, after I did the orientation, I was overwhelmed,” he said. “I thought, am I getting over my head? I was just a soldier, and now I’m something different.”
He was shadowing another employee when he suddenly realized that the system he would be using as a production scheduler at Mars was exactly the same system he used every day when ordering supplies and managing logistics in the Army.
“I looked at the system, and I was totally relieved,” said Schlieper. “All that stress went away, and I was like, I know this. I can do this.”
Today, Schlieper is deeply immersed in his new industry. He feels it’s a good fit for former members of the military, who will have an easier learning curve as a result of their training.
“Before I retired, some people I knew thought manufacturing jobs were jobs nobody wanted,” he says. “But that’s really not the case. It’s completely different. It’s a whole new world.”
Learn more about the Manufacturing Institute’s Heroes MAKE America program.
Job Growth Sluggish in May, Highlighting Need for Certainty
The U.S. economy created just 75,000 new jobs in May, with a sluggish 3,000 manufacturing jobs created for the month.
U.S. manufacturers have experienced record growth over the past couple years, but certainty on a wide portfolio of issues, from infrastructure to trade, will be critical to keep that growth sustained throughout 2019. For policymakers in Washington, the May jobs reported should make that clear.
According to the latest Bureau of Labor Statistics jobs data, the U.S. economy created just 75,000 new jobs in May, with a sluggish 3,000 manufacturing jobs created for the month.
“Manufacturing employment has been more sluggish than desired for four straight months, coinciding with weaker demand and production activity and lagging behind the robust pace we experienced last year,” NAM Chief Economist Chad Moutray said. “Indeed, manufacturers created 264,000 net new jobs in 2018, the best pace of employment growth in the sector since 1997. Yet, the sector has added only 13,000 employees since February. For those numbers to pick back up, our leaders in Washington must recommit to tackling the issues currently creating uncertainty for businesses and focus on policies aimed at sustaining the vigorous growth the industry saw last year.”
Employment has not been the only indicator that’s lagged behind. Earlier this week, the Institute for Supply Management® said manufacturing activity in May expanded at its slowest pace since October 2016; whereas the competing survey from IHS Markit reflected growth that was the weakest pace in nearly a decade. In addition, manufacturing production has fallen in three of the past four months.
“Manufacturers need certainty,” Moutray said. “Things like ratifying the USMCA, securing a bilateral trade agreement with China, passing a long-term reauthorization of the Ex-Im Bank and enacting a bipartisan agreement to update our nation’s infrastructure are immediate steps policymakers can take that would greatly benefit the industry long into the future.”
Another factor holding back manufacturing growth is the looming workforce crisis—a challenge which continues to be the top concern for business leaders, especially in a tight labor market. The number of job openings in the sector has remained highly elevated, averaging about a half million per month over the past 12 months.
“At the end of the day, despite lower levels of industry growth, manufacturers are still creating far more open jobs than workers ready to fill them,” Moutray said. “That’s putting a damper on job creation as well.” Overall, the labor market remains tight, with the unemployment rate remaining 3.6 percent, the lowest since December 1969.
The Manufacturing Institute, the NAM’s education and workforce partner, is the leading industry authority on workforce development and recognizes the need to grow the qualified manufacturing workforce and close the skills gap. It has a range of programs and initiatives designed to do just that.
“The future of this industry and our economy at large are both tied to the future of the manufacturing workforce,” said Carolyn Lee, Manufacturing Institute executive director. “It’s just one more reason why we at the Institute work so hard every day to support the manufacturing workforce of today and grow the manufacturing workforce of tomorrow.”
Kansas Manufacturer Doubles Its Workforce
"We need laws, like tax reform, that can drive economic growth and drive business.”
Ferroloy, a Kansas-based small business that manufactures ductile and gray iron castings, was once on the verge of bankruptcy. But with the help of tax reform, they have doubled the size of their workforce and are in the process of dramatically expanding their facilities.
Mark Soucie, Ferroloy president and owner, bought the company back in 2017 when it had just 20 employees. The business was struggling to break even due to the collapse of the agricultural market, in which most of their customers were involved. Soucie and his team spent much of 2017 stabilizing Ferroloy. It became quickly evident, however, that the supercharged economy could deliver big gains.
“We could tell in early 2018 that activity was picking up, so we added a second shift and more than doubled our workforce by the end of the year,” Soucie explained.
“Now we are in the early stages of adding over 12,000 square feet to our facilities so that we can de-bottleneck the foundry, increase the size of the company’s machine shop and build an in-house pattern shop, which will allow the company to save money while also adding more jobs to their growing workforce,” Soucie said.
Soucie cited tax reform as a significant driver in allowing Ferroloy’s expansion plans to move faster than they otherwise would. More importantly, tax reform has ushered in the strongest economy in more than a decade, which is impacting Ferroloy by increasing demand for their products.
“To me, tax reform is an opportunity to level the playing field,” Soucie explained. “Large businesses have a significant competitive advantage due to scale and capability relative to smaller businesses. Over 50 percent of our working population is employed in small businesses. If you want small businesses to grow and prosper in this country, we need laws, like tax reform, that can drive economic growth and drive business.”
In Soucie’s eyes, keeping tax reform on the books is a no-brainer.
“I don’t understand why some people in Washington want to roll back something that allows small businesses to compete,” Soucie added. “Maybe it’s me being politically naïve, but economically, tax reform that allows small businesses to compete just makes sense.”
2018 was a record-setting year, as manufacturers reported the highest levels of optimism in the 20-year history of the NAM’s Manufacturers’ Outlook Survey.
“With tools like tax reform and regulatory certainty, manufacturing is thriving – and manufacturers are paying it forward,” Chris Netram, NAM vice president of tax and domestic economic policy, said. “Across the country, manufacturers small and large are hiring new employees, expanding operations, raising wages, improving benefits and more. Tax reform has fueled manufacturing, and the industry is propelling the American economy.”
NAM on Announced U.S. Tariffs on Mexico
Timmons: “These Proposed Tariffs Would Have Devastating Consequences on Manufacturers”
Washington, D.C. – National Association of Manufacturers President and CEO Jay Timmons released the following statement on announced U.S. tariffs on Mexico:
Manufacturers, like so many Americans and like President Trump, are frustrated with our broken immigration system and by the inaction that has led to a true humanitarian crisis. The answer to our broken system is a comprehensive, legislative solution, which manufacturers have offered in ‘A Way Forward.’ We continue to urge the administration and Congress to work together to address this crisis because the problem will not be solved just by blaming other countries. Intertwining difficult trade, tariff and immigration issues creates a Molotov cocktail of policy, and America’s manufacturing workers should not be forced to suffer because of the failure to fix our immigration system.
These proposed tariffs would have devastating consequences on manufacturers in America and on American consumers. We have taken our concerns to the highest levels of the administration and strongly urge them to consider carefully the impact of this action on working families across this country. Manufacturers have been working hard to secure passage of the U.S.–Mexico–Canada Agreement, and the last thing we want to do is put that landmark deal—and the 2 million manufacturing jobs that depend on North American trade—in jeopardy.
We will continue to work with leaders on both sides of the aisle on immigration reform, just as we are working to continue our hard-won progress on the USMCA. We cannot afford to put the livelihoods of millions of Americans at risk at the same time.
-NAM-
The National Association of Manufacturers is the largest manufacturing association in the United States, representing small and large manufacturers in every industrial sector and in all 50 states. Manufacturing employs more than 12.8 million men and women, contributes $2.38 trillion to the U.S. economy annually, has the largest economic impact of any major sector and accounts for more than three-quarters of private-sector research and development. The NAM is the powerful voice of the manufacturing community and the leading advocate for a policy agenda that helps manufacturers compete in the global economy and create jobs across the United States. For more information about the Manufacturers or to follow us on Shopfloor, Twitter and Facebook, please visit www.nam.org.
Future of Manufacturing Depends on Building Workforce
In many ways, manufacturing has never been doing better. Record numbers of manufacturers are optimistic about the future. Many are growing, investing, and hiring. Yet, this success is also fueling a growing crisis: too many manufacturing jobs and not enough workers to fill them.
Carolyn Lee, executive director of The Manufacturing Institute (MI)—the education and workforce partner of the National Association of Manufacturers—helps explain manufacturing’s “skills gap” workforce crisis and what the MI is doing to help solve it.
Carolyn, just how bad is the problem currently?
There are more than half a million open jobs in manufacturing right now, and based on a study by The Manufacturing Institute and Deloitte, 2.4 million jobs could go unfilled and about $2.5 trillion worth of GDP could be at risk over the next decade if we don’t get this under control soon. So this is a problem for manufacturing, yes, but it’s also a problem for the economy overall.
What’s driving it?
There are three main drivers. Some don’t know these jobs exist, some don’t have the right skills to land them, and some just don’t see the point. That last challenge—the perception challenge—is particularly tricky. Many envision manufacturing jobs the way their grandparents remember them. But that really isn’t how modern manufacturing careers look today.
Well, how do they look?
Modern manufacturing careers are increasingly high-tech, high-skill, and high-pay. The possibilities in manufacturing will become even more exciting as Manufacturing 4.0 technology continues to revolutionize the industry. Tomorrow’s manufacturing jobs will increasingly rely upon irreplaceable human skills—things like creativity, critical thinking, design, innovation, engineering and finance—and, by the way, many of these careers don’t require a four-year degree or the debt that can come with it.
What is the Institute doing to address this challenge?
We have a variety of programs designed to excite, educate and empower the manufacturing workforce of today and tomorrow, with a particular focus in four key areas: women, veterans, youth and lifelong learning. We are empowering women already in the industry and giving them tools to inspire and mentor others (STEP Women’s Initiative), we are connecting transitioning service members and veterans to great careers in manufacturing plus arming them with the exact skills and qualifications needed to excel (Heroes MAKE America), we are helping excite the next generation by encouraging companies and educational institutions across the country to open their doors to the reality of modern manufacturing careers (MFG Day), and we are engaged in a variety of initiatives to help current manufacturing workers access training for newer technology-intensive jobs—among many other programs and initiatives.
What can others do to help be a part of the change the MI is trying to enact?
One thing I’d recommend, and something the Institute is working to facilitate, is for people to educate themselves, their families, and their friends on what jobs in manufacturing truly look like. It’s an exciting time to be a manufacturer and there are lots of great opportunities in the industry, so come join us.
STEP Award Winner Leads Teams, Saves Lives
As the North America Deliver Operations Lead at Johnson & Johnson, Elaine Thibodeau’s work helps ensure quality, continuity, preparedness and resiliency across the supply chain. She also serves as an advocate for women in the manufacturing industry and a voice of encouragement for millions of young women and girls who might enter the industry one day.
“I think we need to keep fighting the myth that a manufacturing career doesn’t marry well with having a family,” Thibodeau said. “We need to find opportunities to bring young women into our factories and give them early, positive experiences with the industry.”
Her 30 years of experience at Johnson & Johnson includes time in orthopedics, diagnostics, pharmaceutical manufacturing and consumer medical devices – roles that have come with all sorts of challenges. Earlier in her career, Thibodeau led a team that was tasked with taking over a third-party plant to continue producing an oncology medication that was on the FDAs drug shortage list. By making a deal with a supplier to take over a section of their plant, she kept production running.
Doctors in an advocacy group told Thibodeau how essential the medication was for their patients and how shortages caused them to make difficult decisions. “That always stuck with me – it motivated me every day to do my job well,” she said.
At times, Thibodeau faced immense challenges. After Hurricane Maria devastated Puerto Rico, she worked to get manufacturing up and running, bringing jobs back to the community that was deeply affected and providing vital products to enable employees to take care of themselves.
“Day-to-day life was just physically difficult,” she said. “We had to take care of the people first, making sure they had what they needed to be safe, whether that was a generator or medicines or water or diapers.” In collaboration with site leaders and other businesses in the area, she helped to rebuild the industry and begin the process of renewal.
Thibodeau’s interest in manufacturing began at a young age. As a young girl, she built furniture for her dolls with raisin boxes and pieces of wood she found in her family’s garage. When her father, an electrician, went to work, she would tag along, learning how to trouble shoot, which is a skill that has proven valuable.
“I had building blocks and I liked to sew,” Elaine remembered. “I was always interested in putting things together.” An enthusiasm for math and some encouraging teachers led her to an engineering degree, and after a few years, she was offered her first role at Johnson & Johnson – beginning an exciting career that continues to draw her out of her comfort zone.
“If the new job or the new project doesn’t scare you a little bit,” she said, “you’re probably going to be bored in six months.”
Elaine Thibodeau won a 2019 Manufacturing Institute STEP Ahead Award. This profile was adapted from an original interview for the Input, the NAM’s members-only e-newsletter.