How Smart Glasses Helped a Manufacturer Through the Pandemic
How does an expert in one facility guide an engineer halfway across the country through implementing a new technology? Food and beverage packaging manufacturer Crown Holdings found an innovative answer during the pandemic, when its employees couldn’t travel freely: it equipped them with smart glasses.
This pilot program, the subject of a new case study by the Innovation Research Interchange (the NAM’s innovation division), has shown a great deal of promise. Here’s some of what the company has learned so far.
How it worked: The glasses make it possible for experts to connect with on-site workers in real time, thanks to their built-in cameras, microphones, speakers and high-resolution display. The glasses can even be integrated with Microsoft Teams.
- “When the pandemic started, we were trying to coordinate commissioning activities through email and WhatsApp messaging,” said Crown Holdings Project Industrial Engineer Leon Azzi. “Tasks that normally took two to three days were taking weeks.”
- But with the glasses, “[The workers] could share with each other the PLC (programmable logic controllers) electrical diagrams and pictures using the glasses viewer, and the remote experts could point them to areas to focus on in real time,” said Crown Holdings Digital Optimization Team Head Alberto Rodriguez.
Working out the kinks: The company is still perfecting its use of the glasses, which do need some optimization for a manufacturing environment.
- One issue is with the Wi-Fi, since the glasses need a consistent connection that is sometimes hard to find in a manufacturing facility.
- In addition, the integrated noise cancellation headphones that come with the glasses need some upgrades, as the workplace can be incredibly loud and impede easy communication.
- Workers also found the weight of the glasses on their heads to be uncomfortable at times, especially as they were already wearing other safety equipment.
- And last, the screen in the smart glasses is relatively small, which can make it difficult for workers to read.
The path ahead: Crown Holdings considers the program to be a success and plans to expand its use of smart glasses in other areas, including worker training and the mapping of visual data onto equipment. It also hopes the glasses can improve worker interactions with machines via their voice recognition technology, which could allow remote workers to zoom in or capture photos from afar through voice commands.
Learn more: Read more about Crown Holdings’ experience at the IRI Learning Center.
Manufacturers Support Aid for Eastern Europe
It’s been nearly a year since Russia’s invasion of Ukraine, but NAM partner Project HOPE hasn’t let up on its humanitarian aid efforts. With the generous support of many NAM members, it has helped tens of thousands of people who have seen their lives torn apart by the conflict.
What’s going on: Project HOPE—the global health and humanitarian aid organization on the ground providing relief in Ukraine and supporting refugees in Poland, Romania and Moldova—is delivering millions of dollars in medicines, medical supplies, trauma care training, mental health assistance and more to those in need.
What’s been accomplished: To date, the humanitarian relief organization has:
- Delivered 24 generators to health facilities and 34,000 hygiene kits and nonfood items in Ukraine;
- Launched 10 mobile medical units that have treated more than 35,000 patients in Eastern Europe;
- Partnered with 13 local organizations in Eastern Europe to support emergency response;
- Helped provide medical care to more than 5,800 Ukrainian refugee children in Poland;
- Provided nine child playrooms in Moldova that have provided services to more than 3,750 Ukrainian refugee children; and
- Donated more than 300 wheelchairs and other mobility equipment to refugees and others living with disabilities in Romania and Ukraine.
Helping those in need: “Manufacturers are committed to giving back: saving lives, protecting communities and responding quickly in times of trouble,” said NAM Emergency Response Committee Co-Chair and Senior Director of International Trade and Regulatory Affairs Ryan Ong.
- “That includes efforts to stand with the people of Ukraine through strong support to those providing badly needed help in the region. That’s why we’ve been pleased to support and partner with Project HOPE, which is making a difference on the ground.”
The last word: “We are so grateful for the support of the NAM community who has been an integral partner in our Ukraine response,” said Project HOPE Executive Vice President of Global Health Chris Skopec.
- “As we approach the one-year anniversary of the Russian invasion of Ukraine, we at Project HOPE remain committed to continuing to deliver medicines, medical supplies, mental health support and other urgent assistance for the people of Ukraine.”
Get involved: If you’d like to donate to those in need in Ukraine and the region, you can do so via the NAM’s partnership with Project HOPE. For more information about NAM efforts or to share what your company is doing, contact the NAM Emergency Response Committee at [email protected].
The Top 8 Manufacturing Trends for 2023
The NAM recently released its Top 8 Manufacturing Trends for 2023—a guide to the opportunities ahead and the resources that the NAM can offer. Here is what to look out for this year and beyond.
Advanced and emerging technology: Manufacturers are investing in a multitude of new technologies, including artificial intelligence, virtual reality, machine learning and more. Automation and robotics are enhancing workers’ abilities but will also require many more high-skilled employees. Though the workforce shortage is a challenge, digital technologies will help manufacturers become more resilient, efficient and profitable.
- NAM resources: How do you maximize these opportunities? The NAM has resources for you, including the Manufacturing Leadership Council (the NAM’s digital transformation arm), the Innovation Research Interchange (the NAM’s innovation division) and the MLC’s Manufacturing in 2030 Project.
Supply chain resilience: As manufacturers face long lead times, increased costs and a scarcity of raw materials, they are taking steps to boost supply chain resilience through reshoring, cybersecurity, increased supplier pools and more.
- NAM resources: Manufacturers can benefit from resources like CONNEX Marketplace, which helps connect nearby manufacturers and suppliers; the NAM’s Supply Chain Hub—a continually updated collection of webinars and policy documents focusing on supply chain issues; and useful case studies highlighting best practices.
Talent disruptions and opportunities: Manufacturers are confronting a range of challenges around the workforce, including labor shortages and skills gaps, while also figuring out how to take advantage of previously untapped talent pools.
- NAM resources: If you are searching for ways to enhance your employee benefits, The NAM Manufacturers Retirement 401(k) and Savings Plan offers manufacturing employees secure benefits for the future, while Innovation Management Workshops give manufacturing leaders the skills to build innovative and creative teams. Meanwhile, the Manufacturing Institute—the 501(c)3 nonprofit workforce development and education partner of the NAM—promotes a range of events and initiatives designed to expand and diversify the manufacturing workforce as a whole.
Cybersecurity: The threat from bad actors is real, and strong cybersecurity has become critical to manufacturing operations up and down the supply chain. At the same time, manufacturers will have to be on the lookout for new cybersecurity reporting requirements.
- NAM resources: The NAM can help, with support like the NAM’s complimentary Cyber Risk Assessment. NAM Cyber Cover offers cyber insurance and risk mitigation, and you can check out these videos from manufacturing executives laying out best practices for cybersecurity defenses.
Post-pandemic growth and expansion: Long-term goals shouldn’t be downgraded, despite an uncertain economy. Manufacturers should keep pursuing technological advances, navigate government incentives and stay open to mergers, acquisitions and other investments.
- NAM resources: The NAM Incentives Locator helps manufacturers find funds and tax credits to help their business, while the MLC offers networking opportunities for manufacturing leaders.
Tough economic outlook: There’s no doubt that manufacturers face economic headwinds. That means manufacturers need to look for ways to be nimble and responsive to changing realities and able to work more efficiently than ever.
- NAM resources: Tools like NAM Shipping & Logistics give manufacturers discounts on shipping and freight, while NAM Energy offers conversations with energy advisers who can help adjust energy use strategies. IRI Coffee Houses promote virtual conversations with innovation leaders to discuss new developments and opportunities.
Sustainability: Manufacturers are committed to strengthening operations and maintaining a healthy planet at the same time. More than ever, manufacturing companies are looking for ways to reduce carbon emissions.
- NAM resources: The NAM provides resources that can help manufacturers with innovating for sustainability, as well as rethinking end-of-life technology value. Manufacturers can also learn about how digital solutions drive sustainability in manufacturing.
Looking ahead to 2030: Changes in the manufacturing industry and in the world around us—from population growth to the rise of a new middle class to increased interconnectivity—have manufacturers planning for big changes in the next decade.
- NAM resources: The IRI offers a forum for manufacturers to connect with R&D leaders, while the MLC’s Next Phase of Digital Evolution report shows how manufacturing leaders can plan their long-term futures.
Learn more: Take a look at the full guide for more details and to find out more about the NAM resources that will help manufacturers deal with these key trends.
How Manufacturers and Suppliers Can Find Each Other
With supply chains in flux across the country and around the world, manufacturers frequently face obstructions that can hold up their operations and delay critical deliveries.
That’s where CONNEX Marketplace can help.
What it is: Built in collaboration with the NAM, manufacturers and other manufacturing associations, CONNEX Marketplace is a one-stop shop that brings together U.S. manufacturers and suppliers in one clear, verified and searchable database—offering a full picture of the supply chain and helping manufacturers and suppliers find the partners they need.
Why it matters: Especially at a time when supply chains are increasingly complex and constantly under strain, it’s important for manufacturers to understand the full journey of their products.
- By providing manufacturers with detailed data visualization tools as well as blacklist verification, CONNEX helps manufacturers reduce risks in their supply chains and avoid problematic routes and purchases.
How it works: Comprehensive local and national search tools offer manufacturers the opportunity to post their needs and to connect easily and quickly with suppliers using criteria including capabilities, equipment, processes and materials.
- By matching needs with available supplies, the site also helps manufacturers find alternate suppliers when necessary and improve the diversity and resiliency of their supply chains to guard against shocks and snags.
Governors support it: State leaders across the country are speaking up about the power of CONNEX, laying out the value of the program and urging manufacturers to get involved.
- “I think what you’re hearing here with CONNEX … you’re hearing the doors opening on great opportunities for Wyoming,” said Wyoming Gov. Mark Gordon. “It’s gonna expand our footprint regionally, nationally and globally.”
- CONNEX “better connects the Utah manufacturing industry, shortens and reduces supply chain costs and provides new business opportunities to Utah manufacturers and suppliers,” said Utah Gov. Spencer Cox.
- “CONNEX is hugely important,” said Oklahoma Gov. Kevin Stitt. “We’re trying to get everyone to look on this CONNEX website.… If you’re not on that and you’re a manufacturer in Oklahoma, we encourage you to engage with that.”
What we’re saying: “This one-of-a-kind tool empowers manufacturers of all sizes, both buyers and sellers, to be found, increase supply chain optimization and mitigate risk,” said NAM President and CEO Jay Timmons. “It’s a game-changer for U.S. manufacturers.”
How Will AI Impact the Manufacturing Workforce?
AI is changing the way manufacturers do business—from the production line to the back office and across the supply chain. At the Manufacturing Leadership Council’s Manufacturing in 2030 Project: Let’s Talk about AI event last month in Nashville, Tennessee, panelists discussed how those sweeping changes would alter, and enhance, the manufacturing workforce.
A collaboration between the MLC (the NAM’s digital transformation arm) and the MI (the NAM’s 501(c)3 workforce development and education partner), the event provided key insights for manufacturers into how technology and workforce trends interact with each other. Here are a few key takeaways.
Net positive: “The history of technology adoption is about improving the job quality of individuals on the shop floor. AI helps them to do the job better, provide them with better tools, gives them greater authority and ultimately increases the value-add of their jobs. All of that is a net positive for those individuals,” said MI Vice President of Workforce Solutions Gardner Carrick.
- By leveraging data and enabling greater efficiency, AI will improve communication, increase collaboration across disciplines and stimulate innovation, according to the panel.
- In addition, “AI can even inform the workforce’s creativity by working with it to design a new product or system,” said Jacey Heuer, lead, data science and advanced analytics, Pella Corporation.
Skills needed: While you might expect that implementing AI requires workers skilled in programming, data science and machine learning, manufacturers will also need to expand their bench of critical thinkers and problem-solvers. The panelists had a few tips to help companies along.
- Invest in upskilling programs to make the AI integration process at your company smoother and develop the talent you already have.
- Update job descriptions to reflect the skill sets the company will need in the next five to seven years.
- Consider recruiting for and teaching adaptive skills—skills that enable individuals to adapt easily to changing demands and environments—which can increase the flexibility of your workforce.
- Build partnerships with local schools, community colleges and technical and vocational schools to develop talent pipelines that will meet your needs.
The human-AI collaboration: While AI will take over monotonous, repetitive tasks, the panelists predicted that the industry will continue to center around human labor.
- “You can teach AI to do X. You can teach AI to do Y. [However,] combining the two may be really difficult for AI, while a human can do it better. You’re going to continue to see humans in roles that center on making decisions and telling stories,” said Asi Klein, managing director, industrial products and organization transformation, Deloitte Consulting.
- Meanwhile, AI adoption will likely lead to an increase in available jobs, as more skilled workers will be needed to guide and inform these new processes.
The last word: “Over the last 12 years, we’ve seen a lot of technology adoption, but we have not seen a lot of job loss. In fact, we’ve seen job gains,” said Carrick. “There is a lot of opportunity to reimagine jobs to add value that AI will help to illuminate.”
How Digital Manufacturing Creates Business Opportunities
It’s time to think way outside the proverbial box, according to the Manufacturing Leadership Council, the NAM’s digital transformation arm. In fact, as we get closer to 2030, manufacturers are creating entirely new boxes—including new digital business models, products and services, revenue streams, ways to serve customers and opportunities to increase competitiveness.
Collaborative innovation: By 2030, metaverse technologies will provide rich virtual environments for the collaborative development of new ideas. These shared virtual spaces will enable contributors from multiple remote locations to collaborate in real time.
- These collaborations may include manufacturers, partners, academic institutions and research institutes.
- New concepts can be tested in a virtual world before moving to physical prototyping or production.
Outcome-based products and services: As digital platforms mature and products become increasingly smart and connected, the decade ahead may see a boom in more outcome-based services. This is where the customer doesn’t buy a physical product, but instead signs up to pay for the guaranteed outcomes that product or system delivers.
- This shift will require manufacturers to establish new infrastructure rich in predictive analytics, remote communications and consumption monitoring.
- It also requires a mindset change for traditional manufacturing, from a focus on units and costs to product lifecycles, performance levels and usage.
Blockchain networks: By 2030, blockchain could be leveraged for most world trade, helping to provide the secure traceability and provenance needed to prevent physical product counterfeiting, grey markets in medicines and even the adulteration of the global food supply chain.
- A blockchain is an electronically distributed ledger accessible to multiple users. Blockchains record, process and verify every transaction, making them safe, trusted, permanent and transparent.
- Blockchain technologies promise to be a viable solution to manufacturers’ need to automate, secure and accelerate the processing of key transactions across industrial ecosystems.
E-manufacturing marketplaces: Digitally empowered production-line adaptability, such as the kind that emerged during the pandemic, will provide a foundation for companies to offer spare production capacity to other companies in different sectors.
- This maximizes the return on a company’s production-line investments and can generate new revenue streams for the future.
- Combined with e-commerce, e-manufacturing will enable designers, engineers and/or smaller companies to more easily connect with a large pool of qualified producers to deliver and scale a final product.
Manufacturing in 2030 Project: New Boxes is just one of the industry trends and themes identified by the Manufacturing in 2030 Project, a future-focused initiative of the MLC. For more details on megatrends, industry trends and key themes for Manufacturing in 2030, download the MLC’s new white paper “The Next Phase of Digital Evolution.”
Top Manufacturing Tech Trends of 2022
Now that 2023 is here, we’re looking back on 2022’s top tech trends in manufacturing. The NAM’s digital transformation arm, the Manufacturing Leadership Council, and its innovation management division, the Innovation Research Interchange, gave us an overview.
AI everywhere: From automatically responding to shifts in production demand to anticipating breakdowns in the supply chain, artificial intelligence showed up more than ever before throughout manufacturing operations.
- More than two-thirds of manufacturers are either using AI now or will be doing so within two years, according to MLC research.
- Current use cases include predicting needed maintenance for equipment, forecasting product demand and monitoring performance metrics such as productivity and efficiency. Future use cases could include fully autonomous factories that run continuously with minimal human intervention.
Training on demand: Training for technicians and frontline operators used to mean time in a classroom with a live instructor. In 2022, more manufacturers turned to virtual, on-demand learning tools that allowed workers the freedom to learn at their own pace.
- This ran the gamut from video content libraries to immersive augmented reality/virtual reality experiences that guide and correct trainees.
- In 2023 and beyond, this type of learning experience will be essential to attracting and retaining younger workers who are familiar with digital learning and want the latitude to gain new skills on their own schedules.
Digital twins: Manufacturers used digital twins—virtual models designed to reflect a physical object, system or process accurately—to create design prototypes and test their performance.
- Digital twins will continue to allow for new levels of design optimization, improved product development and performance and significant waste reduction for manufacturers.
Robotic collaboration: Once confined to steel cages and bolted to floors, industrial robots took center stage in 2022.
- No longer limited to repetitive tasks and kept far from human workers, new-generation robots are safe enough to work alongside employees, can be moved quickly around shop floors and are programmed easily to do multiple tasks.
- Since they’ve also become more affordable, they’re an economically feasible investment for companies of all sizes.
Cybersecurity as safety: A rise in connected factories also meant a rise in cyberattacks on manufacturers. In an industrial setting, a cyberattack can be very dangerous, as it can cause equipment to malfunction.
- Last year, more companies began addressing the threat with cyber drills, tabletop exercises for simulated attacks and other training exercises designed to keep businesses—and workers—safe and secure.
Low-code/no-code development platforms: In 2022, more manufacturers embraced the use of mobile and web apps to build applications quickly. Using these platforms, enterprise and citizen developers can drag and drop application components and connect them to create apps—without line-by-line code writing.
- Business teams with no software development experience built and tested applications without any knowledge of programming languages, machine code or the development work behind a platform’s configurable components. We can expect to see more of it this year.
Smart glasses move beyond the pandemic: Many manufacturers kept up their pandemic-era use of smart glasses, which they had used to troubleshoot issues on the ground when travel was restricted and engineers and technicians couldn’t reach sites.
- They also expanded smart glasses’ use to include scanning sensor data so users can see visual data “mapped” onto equipment to better identify issues and fixes.
Interested in learning more? Check out the MLC and IRI for more insights into manufacturing’s exciting, high-tech future.
Sustainability Is a Top Manufacturer Priority, Survey Shows
Manufacturers are pursuing sustainability like never before.
That’s according to recent polling conducted by the Manufacturing Leadership Council, the NAM’s digital transformation division. The annual Sustainability and the Circular Economy research survey seeks to determine the progress made in sustainable manufacturing.
Competitiveness: There has been a surge in the number of manufacturing executives who view sustainability as critical to the future of their businesses.
- 58% of respondents in 2022 believe sustainability is essential to future competitiveness compared to 38% in 2021.
- 68% of executives say they are implementing extensive, corporate-wide sustainability strategies. That’s up from just 39% in 2019.
What’s driving change: The motivations go beyond regulatory compliance and cost savings.
- 78% say sustainability is about better alignment with corporate values.
- 68% believe in creating a cleaner, healthier environment.
- 66% seek to improve company reputation with customers and investors.
Top corporate goals: More than half of survey respondents reported having specific sustainability goals and metrics across almost all key functions in the company.
- Goals were most apparent in manufacturing and production (79%), supply chain (69%) and product design and development (67%).
- Additional goals were cited in transportation and logistics (56%) and partner compliance (51%).
Energy efficiency is No. 1: The primary sustainability focus of manufacturers, according to survey results, is energy efficiency and reduction, combined with the transition to renewable energy sources. These efforts are linked intrinsically to meeting net-zero emissions goals.
- 45% of respondents report having announced formal net-zero goals.
- 30% aim to hit net zero by 2030.
Digital tech, employee training play a role: Also on the rise is the number of companies that recognize the importance of digital solutions in their sustainability efforts.
- These tools are being used to manage and monitor materials and energy consumption, optimize operations to improve efficiency and report sustainability progress.
- Respondents also say meeting sustainability targets must include engaging employees through education and training, as well as greening their supply chain.
The last word: An overwhelming 90% of all respondents agree that manufacturing has a special responsibility to society to become more sustainable and accelerate the transition to a future circular industrial economy.
Interested in putting some renewable energy solutions into action, including solar power, battery storage and LED lighting? Programs from utility companies and other entities enable efficiency upgrades with little or no upfront capital. Connect with NAM Energy to explore your options!
How a Manufacturer Uses R&D to Keep Old Jets Flying
What does the U.S. military do when an expensive asset like a plane or a weapons system begins to break down?
Often, it turns to companies like Parts Life, Inc.—an innovative manufacturer that can reverse-engineer obsolete parts and help find solutions for hard-to-replicate products. But after a tax law change went into effect in 2022, the New Jersey–based manufacturer is facing increased costs for research and development, creating a barrier to the kind of innovation that is the focus of its business.
The change: Until the beginning of 2022, businesses could deduct 100% of their R&D expenses in the same year they incurred the expenses. Starting this year, however, a tax law change requires businesses to spread their deductions out over a period of five years, making it more expensive to invest in growth and innovation.
A focus on innovation: For Parts Life, coming up with new ideas is an essential, daily activity.
- “Parts Life is built around being a solutions provider,” said Parts Life President and CEO Sam Thevanayagam. “We are providing solutions for very expensive and mission-critical assets that are extremely strategic for the defense of the nation, but are also older—so their parts are not necessarily being supported.”
- “That’s where we come in to do reverse engineering. So, we’re looking at an old problem, but using innovation to solve it going forward.”
A benefit for savings: By helping the military extend the life of its assets, Parts Life also helps taxpayers.
- “We’re taking care of the warfighter and the taxpayer,” as Thevanayagam puts it.
A look ahead: As global conflicts shift, the U.S. military needs suppliers like Parts Life to help it develop solutions for future challenges, too.
- “Right now, our military is coming out of conflicts in Afghanistan and Iraq, but future conflicts may involve different terrain with different problem sets,” said Thevanayagam.
- “The work that we are doing today is helping them figure out how to approach those challenges. We’re having them tell us where they need to be, and then we’re helping them with the innovation they need to be successful.”
A tough choice: With the change in tax law, companies like Parts Life will be forced to make difficult decisions about how to spend scarcer resources, harming their ability to do critical, forward-looking work.
- “Currently, we’re leaning forward in resources and talent to lead the future,” said Thevanayagam. “If the government is going to pull the rug out from under us, we’re not going to be able to be aggressive. We’ll have to focus on maintaining our business rather than investing in new innovation.”
Our take: The NAM has pushed forcefully for the tax change to be reversed—and in October, told policymakers that the R&D amortization provision poses a “serious threat to our national security,” in part because of its impact on manufacturers like Parts Life that supply and support the U.S. military.
The bottom line: “The only way for us to continue to be relevant is to make sure that we’re investing in innovation and seeing what we can do to be a part of designing the future,” said Thevanayagam.
Visit the NAM’s R&D Action Center for critical R&D policy updates, industry stories and an opportunity to engage directly with your members of Congress.
Sargento Makes a 10-Year-Old Boy’s Wish Come True
On Dec. 21, 2021, the Ball family from Winston-Salem, North Carolina, received devastating news: their son Maxx had Ewing sarcoma, a rare form of bone cancer that typically occurs in children and young adults.
Maxx’s wish: As he battled the potentially life-threatening disease, 10-year-old Maxx, whose cancer is now in remission, had one wish: to travel to Wisconsin to learn about the cheese-making process.
- “Most kids choose Disney World or a trip to Hawaii, but not my son,” said his mom Lauren. “He loves cheese and all things dairy, so he wanted to come to Wisconsin.”
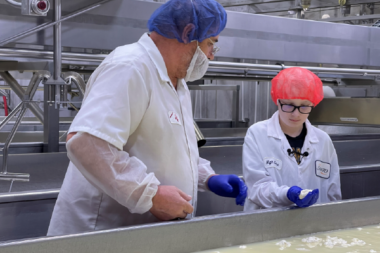
From wish to reality: The Make-A-Wish Foundation contacted Plymouth, Wisconsin–based Sargento—a leading manufacturer of shredded, sliced and snack natural cheese products—which was thrilled to grant Maxx’s wish.
Sargento has been a longtime supporter of the Make-A-Wish Foundation, partnering with other local businesses on an annual golf-related fundraiser that provides substantial support for Make-A-Wish Wisconsin. Sargento’s Executive Vice President of Operations and third-generation family owner, Mike McEvoy, has also served on the board of Make-A-Wish Wisconsin.
The itinerary: After arriving in Madison the Friday before Thanksgiving, Maxx and his family visited the Center for Dairy Research at the University of Wisconsin–Madison. He also met Wisconsin Gov. Tony Evers, visited
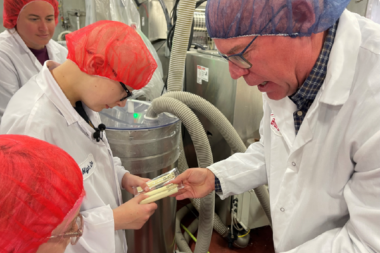
the Wisconsin State Capitol building, checked out the House on the Rock and then traveled to Green Bay to tour Lambeau Field. But the final day of his Dairyland tour was a stop at Sargento’s new location: Baker Cheese in St. Cloud, Wisconsin.
The visit: Sargento General Manager Brian Baker and Master Cheese Maker Jeff LeBeau provided a tour of the facility and explained the cheese-making process in detail. Maxx helped with making cheese curds, learned the documentation process and even operated one of the facility’s computer systems.
- “On our tour, he kept saying, ‘This is awesome,’” said Baker. ‘It really put Thanksgiving into perspective. They are a wonderful family, and what he’s gone through, to be here and to be so engaged and on the other side of his diagnosis, shows what’s really important.’”
The last word: “It was a great day, and it was a pleasure to help make Maxx’s wish come true,” said Sargento Vice President of Human Resources and Community Relations Karen Lepisto.